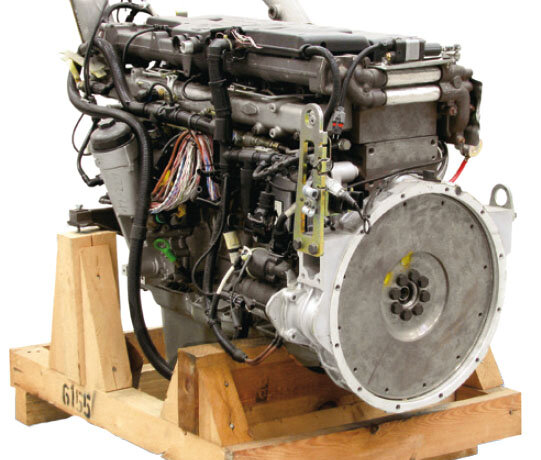
Engine installation and initial start-up
checklist for avoiding consequential faults
Information on use
Is the engine not working after the repair? What damage may occur when the engine is started for the first time? What mistakes can be made during the engine repair? And how can consequential faults be avoided? You will find an exact description of what to do in this article.
SITUATION
Severe damage often occurs following an engine repair. Faults that are not resolved in the periphery of the engine, whether mechanical or electrical, can lead to costly consequential faults. With the following checklist, the majority of possible sources of trouble can be eliminated during engine installation.
Engine mechanics
Components |
Activity |
Background |
Intake system |
Check, clean |
There may still be fragments, metal chips or other soiling in the intake system from engine damage. |
Charge air cooler |
Clean or |
Following engine damage, there are often large quantities of engine oil in the charge air cooler. |
Turbocharger |
Check, clean, |
Supply and return lines are blocked with carbon due to thermal influences, the resulting inadequate oil |
Turbocharger |
Check, replace |
The turbine and compressor impellers must be in impeccable condition, they must not be deformed or |
Oil filter, oil cooler and |
Clean or |
Metal chips resulting from engine damage can be flushed to the clean side of the oil filter. Thoroughly |
Oil system |
Fill |
After you have connected it to all components supplied with pressure oil (oil cooler, turbocharger, |
Exhaust system |
Check, clean, |
As a result of engine damage, fragments of pistons, valves and the turbocharger, as well as fuel and oil, |
Fuel filter and filter |
Check, clean |
Injectors and high-pressure pumps in diesel engines are extremely sensitive to fuel contamination. |
Fuel/ |
Check, replace |
Filling the tank with the incorrect fuel frequently leads to engine damage. If there is any uncertainty |
Cooling system |
Clean |
Before installing the engine, rinse cooling system components remaining in the vehicle with clean water. |
Coolant agent |
Replace |
Only use specified coolant agent in the correct dilution. Do not start up the engine, even briefly, without |
Before starting the new engine
Components |
Activity |
Background |
Electric |
Check |
Check correct connections using a circuit diagram of all vacuum lines and electrical plug-in connections. |
Engine |
Start |
Before starting up the engine, oil pressure must be built up. If necessary, take suitable action to ensure |
Engine |
After start-up |
After start-up, do not damage the engine through repeated early acceleration. The oil system needs some |
Electronic components
Components |
Activity |
Background |
Engine control unit(s) |
Fault check |
Read out the fault code memory, note the diagnostic trouble codes and then delete the fault code |
Engine electronics with |
Actuator test |
The actuator test is used to check the function of the relevant components. |
Carry out |
Adapt, teach in |
Today, many components have to be adapted following replacement. These include, for example: |
Common rail injectors |
Programming |
After being swapped or replaced, common rail injectors must be programmed in the control unit |
Test run/finishing work/final inspection
Components |
Activity |
Background |
Test run |
Note OBD |
The test run should incorporate a cold start, warm-up, urban traffic, driving on a highway and a |
Fault code memory |
Check, delete |
Always check and delete the fault code memory before and after the test run, even if the MIL (malfunction |